Quality Assurance
Our quality management system is certified to ISO 9001:2015 standards, demonstrating our dedication to continuous improvement and ensuring customer satisfaction. Our quality objective is to maintain a finished product pass rate of at least 95%, an on-time delivery rate of at least 90%, and a customer satisfaction level of at least 90%.
Quality Assurance
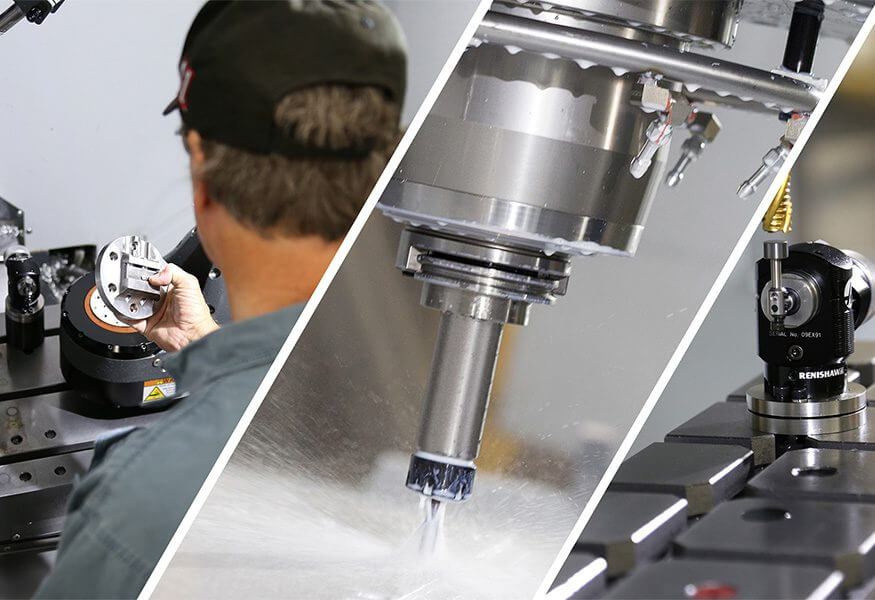
Continuous Improvement in Custom Manufacturing
At KevoRapid, we are dedicated to continuously improving and optimizing our custom manufacturing capabilities, from prototype to production. This includes CNC machining, rapid prototyping, and rapid tooling. Our commitment extends to quality control processes, where we strictly adhere to the ISO 9001 certified quality management system.
Through standardized production procedures, work instructions, and advanced testing equipment, we meticulously measure and inspect each production step to ensure your project meets stringent quality specifications.
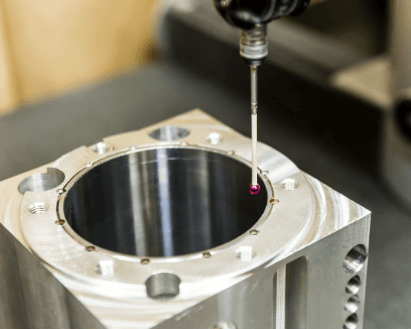
Our Quality Policy
Optimizing Management and Boosting Efficiency
At our organization, we prioritize the implementation of standardized and scientific management concepts. We develop rational working methods and operating codes, ensuring efficiency and effectiveness. Furthermore, we invest in training exceptional employees, equipping them with top-notch skills. Our ultimate goal is to continuously enhance production efficiency.
Driving Operational Excellence for Customer Satisfaction
We are driven by the expectations and values of our customers. To exceed their expectations, we consistently enhance our operation and management. This involves optimizing production planning, refining processes, streamlining supply chain coordination, controlling production costs, and nurturing skilled staff. Through our unwavering commitment to continuous improvement, we strive for excellence and aim to continuously enhance customer satisfaction.
Fostering a Learning Culture for Growth and Innovation To foster growth and innovation, we are dedicated to building a learning organization. This involves implementing a knowledge management system to collect and organize valuable insights from professional technicians, departments, business data, and production experiences. These resources serve as crucial references for implementing corrective and preventive measures and enhancing production technology. Additionally, we prioritize continuous training for our employees, encouraging them to share their experiences, promoting innovation, and strengthening the cohesion of our company.
Striving for Quality Excellence
Through the implementation of our robust quality management system, we prioritize strengthening quality control and inspection at every stage of production. This not only optimizes our company’s processes but also fosters effective communication between customers and departments. Additionally, we invest in training our employees to enhance their quality awareness, driving continuous technological advancements and the efficient manufacturing of high-quality products.
Inspection and Control Procedures
From RFQs to Shipment: Ensuring Reliable Quality
Our commitment to quality spans the entire project, from RFQs to shipment. To kickstart our quality assurance, we conduct two independent reviews of the purchase order, ensuring seamless coordination in dimensions, material, quantities, and delivery dates. Experienced personnel involved in setup and production meticulously review and create individual inspection reports for each required operation. We carefully document any special quality needs and instructions, assigning inspection intervals based on tolerances, quantities, or part complexity. Through diligent tracking and analysis of every manufacturing step, we minimize part-to-part variation, guaranteeing consistent and reliable quality for every part, every time.
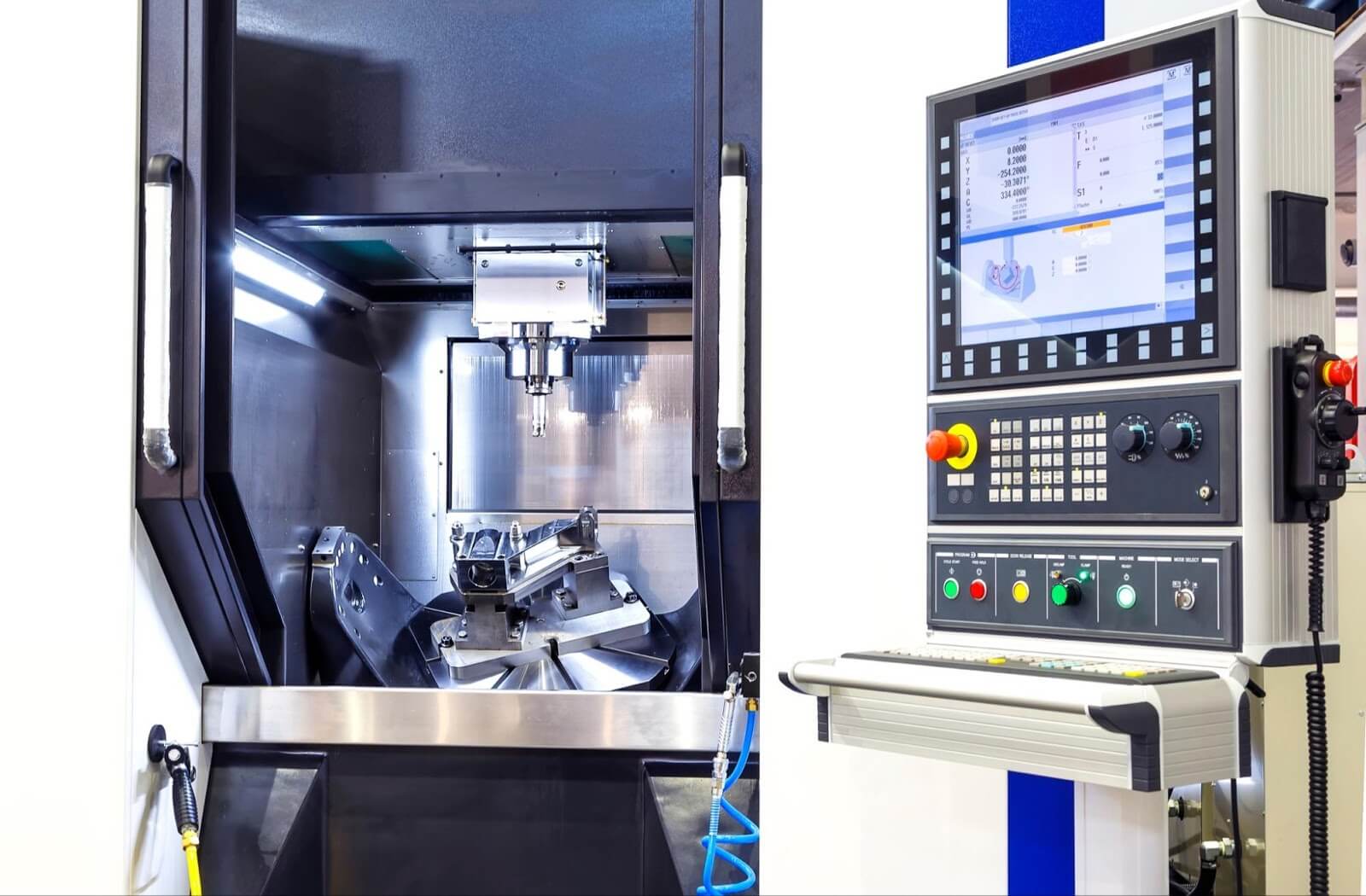
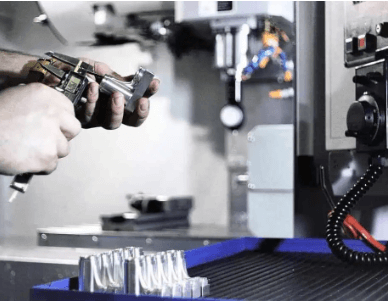
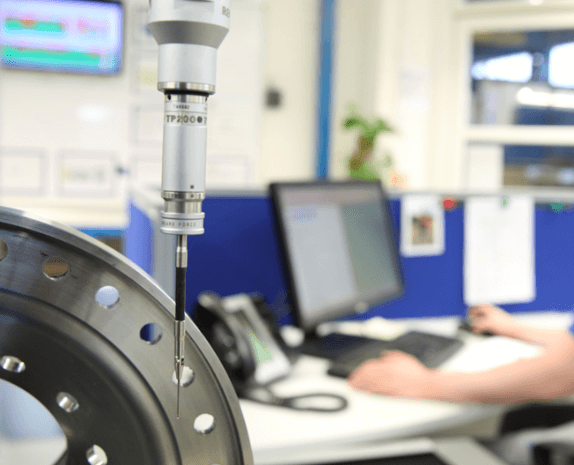
Ensuring Quality Excellence in Rapid Manufacturing
Our dedication to consistent quality control spans from part to part, product to project. We prioritize attention to detail, problem-solving, research on new materials and processes, and investments in technology. Additionally, we are committed to building and sustaining a team of professional rapid manufacturing experts.
- Comprehensive Design for Manufacturing (DFM) review for all projectsThorough evaluation of contracts and purchase orders
- Rigorous assessment of production capacity and planning (PMC)
- Thorough inspections of incoming raw materials
- Regular sampling and in-process inspections (IPQC)
- Efficient management of nonconforming products through corrective and preventive actions
- Thorough final inspections and testing with detailed reports and required certifications (OQC)
- Regular customer satisfaction surveys to ensure we consistently exceed expectations
Quality is Our Policy
- Implement a robust Management System to effectively meet customer needs and comply with regulatory requirements.
- Establish clear Quality Objectives that are regularly reviewed to assess the effectiveness of the Management System in achieving these objectives.
- Provide ongoing employee training programs focused on enhancing the quality of products, services, and systems.