The constantly changing market needs have necessitated faster and more accurate fabrication of products. CNC machine shops are a product of this industrial revolution. A CNC machine shop continuously advances and invests in technologies to achieve the highest efficiency in manufacturing products. They provide CNC machining services to various businesses for different applications.
This guide gives detailed information about everything you need to know about CNC machine shops and how to find the right partner for your manufacturing projects.
What Is A CNC Machine Shop?
A CNC machine shop is a specialized facility or building where CNC machining operations occur. A machine shop can be a massive standalone shop or a section of a larger factory dedicated to meeting the needs and demands of customers. It houses various CNC machines used in machining different simple and complex parts using subtractive techniques.
The machine shop uses materials such as plastic, metals, composites, wood, etc., to form different custom parts using various machining processes. Several industries, including automotive, aerospace, medical, military, and many more, depend on CNC machine shops due to their vast on-demand manufacturing capabilities.
What Will You Find In A CNC Machine Shop?
Although CNC machining workshops are of varying sizes and specialties, there are typical machines or equipment that would be in a standard one. Here are some of them:
1. CNC Milling Machine
A CNC mill is one of the most versatile machines you will find in a CNC workshop. This machine is commonly used in subtractive machining operations. The milling machine uses a rotating cutting tool to remove material from different materials. The machines have varying milling cutters featuring 3-, 4-, 5-, and 6-axis configurations. As a result, the milling machine can execute varying cuts from threading to roughing.
2. CNC Lathe Machine
Generally, a lathe is a machine operated manually by a machinist. However, CNC (computer numerically controlled) lathes are commonly used in a CNC machining shop. It works oppositely as a milling machine. When using a lathe, the workpiece material rotates while the cutting tool moves around the workpiece in a linear pattern making designated cuts. These CNC lathes are often used for grooving, facing, knurling, and sanding operations.
3. Grinding Machine
A grinding machine uses a high-quality grinding abrasive wheel made of small hard particles to shave off small layers of materials and form a very precise dimension with great or mirror-like surface finishes. Such operations are used for high-precision parts and it is recommended to use them only for tolerances IT 7 or higher. They are costly and take up time.
4. Drill Press
It is a mounted drill type with precise movement and is often controlled by a lever. A drill press is more stable and powerful than handheld drills. Although the drill press works similarly to a regular press, it can be used for different manufacturing operations besides drilling holes.
5. EDM Equipment
Electrical discharge machining equipment is used in a machining process that uses electrical current to erode or vaporize particles from the surface of a workpiece material. The EDM process is an ideal solution for machining hardened pieces because it does not involve the application of force on the parts. Surface Finishing Tools
When the parts are complete, you sometimes need to get additional properties. Such as mirror-like surface finishes, colors, glossiness, or smoothness. All of them require special treatment so a good CNC machine shop usually has at least a small set of post-processing equipment. Some CNC shop manufacturers also offer polishing, bead blasting, and anodizing services.
6. Bandsaw
A bandsaw is a multipurpose cutting machine for making straight cuts in a workpiece. CNC machine shops use the bandsaw to process raw materials into smaller pieces before further cutting. Generally, CNC machine shops receive long bars and slabs that require certain cutting operations before machining. Machinists often use the bandsaw in such situations.
7. 3D Scanner
Machinists move the 3D scanner around the workpiece to capture its different parts and provide its 3D model. With this model, manufacturers can quickly tell whether a workpiece is compatible with a machining process. The process usually takes 3-4 minutes.
8. Coordinate Measuring Machine (CMM)
A coordinate measuring machine is a fundamental tool in achieving high-quality results. It helps to measure the geometry of parts to ensure that the machined parts meet the original dimensional requirements. CNC machining workshops need to confirm dimensions and tolerances together with other properties. Hence, a coordinate measuring machine is vital to ensuring the accuracy of almost any geometry.
9. Micrometer and Pin Gauges
The micrometer is also an effective precision measurement tool. Manufacturers often use the micrometer to measure different dimensions, such as the machined part’s thickness, length, and depth. It is versatile and more reliable than most measuring tools. On the other hand, pin gauges are ideal tools for inspecting the diameters and tolerances of small holes in a workpiece.
Advantages Of Using A CNC Machine Shop
The CNC machining shops offer various businesses a wide range of benefits. Here are some of these advantages:
1. Accuracy and Precision
A CNC machine shop helps businesses to create high-quality parts with higher accuracy and precision. The CNC machining shop is the ideal partner for industries with strict requirements for accuracy and precision in machined parts.
In addition, some CNC workshops offer 5-axis CNC machining, which allows the manufacturing of machined parts with high precision requirements.
2. Increased Production Speed
Several businesses benefit from increased production speed due to the automated nature of the machines in the CNC workshops. These machines maintain preprogrammed feeds and speeds, producing parts in small or large-volume at shorter cycle times.
CNC machines, like 5-axis machines, execute manufacturing tasks faster, allowing faster parts production. Therefore, CNC workshops offer lean manufacturing, maximizing productivity while eliminating waste.
3. Reduced Labor Costs
Reduction in the cost of labor is one of the many benefits of using a CNC machine shop. Machines in the CNC workshops use automated (Computer Numerically-Controlled) machines to execute machining tasks.
In common, these machines do not require any manual or human effort in the operations. Consequently, one operator can manage several CNC machines on longer cycles, thereby reducing overall costs.
4. Improved Product Consistency
The G-Code commands the movements of the CNC machines in the precision machine shops. These CNC machines can produce high-quality duplicate parts to tight tolerances without errors since it follows a computer program. The ability of these CNC machines to iterate machined parts helps CNC machine shops improve the consistency of products according to specifications.
Challenges Of Operating A CNC Machine Shop
Although CNC machine shops offer businesses a wide array of benefits, a few challenges may hinder the success of a CNC machine shop. Here are some of these challenges:
1. High Initial Investment Costs
The initial investment costs of running a CNC machine shop are usually high because CNC machines are not so cheap. It is a major challenge for new machine shops that are just starting up and have no old equipment to upgrade. The purchase of CNC machines is not as simple as consumables. More so, operating a CNC machine shop is an investment that only yields profit in the long run.
2. Skilled Labor Shortage
Running a CNC machine shop requires experienced operators to manage sophisticated CNC machines. However, machine shops find it hard to get a better replacement for retiring operators. Likewise, machine shops face several difficulties in locating and training new replacements.
3. Maintenance and Upkeep Costs
The cost of maintaining a CNC machine shop is usually high because the machines there are ultra-modern. Whenever a CNC machine breaks down, its repair is often costly as it requires a complex combination of software and hardware to function correctly. Hence, a breakdown in these systems may necessitate both programming and mechanical expertise to fix.
4. Adapting to Technological Changes
As technology advances, there are significant changes in the pattern for shaping and designing precision metal parts. Artificial intelligence and robotics have taken over what used to be human-only tasks. As a result, CNC machine shops and operators must adapt to the technological changes to use them. Additionally, there is an increase in the requirement for highly skilled operators to manage these new machines.
How To Choose The Right CNC Machine Shop?
As a product developer or business owner, you do not necessarily have to own a CNC machine shop. So, you must partner up with a reliable CNC machining facility with the best machining capabilities for your project requirements. You need to consider these factors whenever you need a particular manufacturing services provider.
1. Competitive Prices
A CNC machine workshop will charge differently depending on experience, size, technology, and other factors. Choosing the right CNC machining shop includes finding a reliable manufacturing partner at a reasonable price. Although CNC machining costs can be a huge burden, compare the prices of different machine shops. However, this should not be detrimental to the machined part’s quality.
Note: Partnering with a machining shop because it offers lower rates could be dangerous. This is because a machine shop that offers you rates that is unprofitable to them is bound to provide products and services below standard. Such a machine shop will surely cut corners to increase its profit margin.
2. Quality and Reliability
Partner with a CNC precision machine shop with experienced machinists, modern CNC machines, and standard measuring equipment. It gives you high assurance over the quality of the machined parts. However, if you doubt a machine shop, give them a call or visit the workshop to tour the facility in person before starting the partnership.
A CNC workshop with a wide range of manufacturing capabilities is better than those with little or nothing to show. However, you should note that most machining shops are not always sincere with their limitations. Thus, it would help to find a shop that is more transparent about its limitations than a shop that promises but fails to meet your project’s demands.
3. Turnaround Time
Time is vital in any manufacturing business because time is money. It is crucial to partner with a 5-axis machine shop capable of saving costs and time. How fast a CNC workshop can deliver your product determines how soon you can profit from your business.
A machining shop that uses CNC technology can significantly reduce production time while offering the most economical means of producing high-quality complex parts quickly. Therefore, ensure that the CNC machine shop you are willing to go into business with can deliver without delay.
4. Confidentiality
Confidentiality is an important attribute you should look out for when partnering with a CNC workshop. These prototype machine shops execute custom CNC machining and other manufacturing operations for businesses. As a result, these workshops need to assure their client/customers that their designs are safe and will be kept private.
However, there are legal means of ensuring confidentiality between customers and these workshops. You can request that your machine shop sign a Non-Disclosure Agreement (NDA) to put everything under check before work begins. Hence, this will help to safeguard your designs from being passed to any other third parties.
Nevertheless, do not hesitate to reject a machine shop that doesn’t agree to sign an NDA.
5. Good Communication
Most machine shops with good communication skills build a steadfast relationship with their customers. You’ll find that they are readily accessible to handle all your design details through diverse media. Aside from this, they use a suitable feedback mechanism and promote the project’s development.
Future Trends Of CNC Machine Shops
CNC machining shops continue to evolve significantly, achieving the once impossible tasks. Precision CNC machining is one of the fast-evolving industries to date. However, the question is – what is the future of CNC machine shops? This section explores the apparent future of CNC machine shops:
1. Advancements in Technology
CNC machine workshops use innovative machines to increase production accuracy and volume while eliminating downtime. These precision CNC machining facilities use special tooling to produce custom products for customers. Consequently, these technological advancements improve the capabilities of a CNC machine shop.
2. Increased Demand for Customized Products
CNC technology has made manufacturing easy, so a CNC machine workshop can manufacture customized products for customers/buyers. Business owners continue to demand complex and personalized products from their manufacturing partners.
However, the sophistication of CNC technologies allows machine shops to handle the demand increase for customized products successfully. It is increasingly easy for CNC shops to manage on-demand manufacturing irrespective of the volume and requirements.
3. Integration of Artificial Intelligence and Robotics
The future of CNC machine shops is deeply invested in integrating artificial intelligence (i.e., machine algorithms) and robotics. Manufacturing engineers are intelligent computers and robots such that machines can execute manufacturing tasks exactly as humans. This integration will positively influence the future of CNC machining in various aspects, such as high accuracy, faster production, efficiency, etc.
4. Emphasis on Sustainability and Eco-Friendliness
Sustainability and eco-friendliness are the primary goals of a CNC machine shop. As such, machine shops practice manufacturing processes that minimize negative environmental impacts and reduce waste. This helps achieve sustainability and eco-friendliness to ensure the safety of workers, save costs, and strengthen competitive positions.
A Reliable CNC Machine Shop – KevoRapid
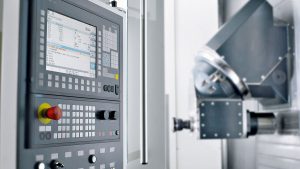
If you are looking for a reliable CNC machine shop to partner with, is the ideal partner for your manufacturing project. we are a professional and trusted provider of rapid prototyping and manufacturing services. We assure quality, precision, and affordability for any volume of machined parts.
Our CNC technology and a team of engineering experts allow us to offer a wide range of CNC machining solutions such as CNC milling services, EDM, CNC turning, and surface treatment finish. Feel free to contact us today, let’s handle your project!